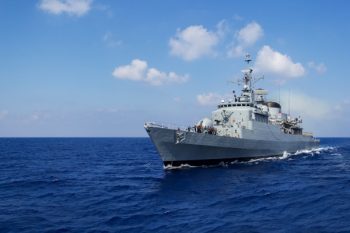
Manufacturing components for marine applications is a complex and demanding process. The harsh ocean environment requires materials that are highly resistant to corrosion and degradation, and the wrong material selection can have catastrophic consequences. Additionally, marine projects often require low-volume production of customised components with high precision and accuracy, making traditional manufacturing methods challenging. This article explores the benefits of 5-axis CNC milling in addressing these challenges and delivering reliable, high-quality parts for complex marine projects.
The Challenges of Marine Component Manufacturing
Manufacturing components for marine applications is a complex and demanding process. One of the most critical challenges is material selection. Marine components must be able to withstand the harsh conditions of the ocean, including exposure to saltwater, UV radiation, and extreme temperatures. This requires materials that are highly resistant to corrosion and degradation. The wrong material selection can have catastrophic consequences, including component failure, system downtime, and even loss of life.
For example, a faulty propeller shaft or malfunctioning navigation system can put an entire vessel at risk. Furthermore, marine projects often require low-volume production of customised components, which can be difficult to achieve with traditional manufacturing methods. The need for high precision and accuracy in these components adds an extra layer of complexity, making it essential to choose a manufacturing process that can deliver reliable, high-quality parts.
The Benefits of 5-Axis CNC Milling for Marine Projects
Five-axis CNC milling technology has revolutionised the manufacturing of complex marine components. This advanced machining process enables the production of intricate shapes and designs with unparalleled precision and accuracy. By utilising a 5-axis CNC milling machine, manufacturers can machine complex shapes from solid materials, such as carbon fibre, which would be impossible to produce through traditional methods. For example, Thompson Precision has successfully machined complex shapes from solid carbon fibre for racing yacht keels, a feat that was previously near impossible.
The economic benefits of 5-axis machining from solid material are also significant, particularly for low-volume production runs. By eliminating the need for pattern making and casting, manufacturers can reduce costs and lead times, making it an ideal solution for prototyping and development requirements prior to production. With a maximum working envelope of 2500 mm x 1500 mm x 1000mm, Thompson Precision’s 5-axis CNC milling machines are capable of producing large, complex components with ease, making them an ideal choice for marine projects.
Applications of Large CNC Milling in Marine Projects
The applications of large CNC milling in marine projects are vast and varied. One of the most significant is in the production of propeller profiles, which are ideal candidates for 5-axis CNC machining. The complex curves and shapes of propellers can be accurately machined using this technology, resulting in improved performance and efficiency.
Additionally, 5-axis CNC milling is particularly well-suited for prototyping and development requirements, allowing designers and engineers to quickly and accurately test new designs and iterate on existing ones. This can significantly accelerate the design-to-production process, getting new marine technologies to market faster. Beyond propellers, large CNC milling is also used in other safety-critical marine applications, such as aircraft, submarines, battleships, and other high-performance vessels. In these environments, the precision and reliability of CNC-milled components are critical to ensuring the safety of crew and passengers.
The Role of Design and Collaboration in Complex Marine Projects
In complex marine projects, collaboration between design teams and manufacturers is crucial to delivering successful outcomes. The design team plays a critical role in solving engineering problems and creating complex components that meet the exacting demands of marine environments. Solidworks software is a powerful tool that enables design teams to model, simulate, and analyse complex components, ensuring that they are optimised for performance, reliability, and manufacturability.
At Thompson Precision, the design team works closely with marine sector customers to solve engineering problems and create complex components that meet their specific needs. By leveraging Solidworks software, the team can rapidly iterate on designs, test virtual prototypes, and optimise component performance. This collaborative approach enables Thompson Precision to deliver high-precision, complex components quickly and efficiently, even in safety-critical environments where quality and speed are paramount. With a stock of materials on hand and the capability to machine urgent components in a matter of days, Thompson Precision is well-equipped to support the fast-paced demands of marine project development.
In summary, large CNC milling has emerged as a critical solution for complex marine projects. By leveraging this technology, manufacturers can overcome the challenges of material selection, low-volume production, and high precision requirements. The benefits of 5-axis CNC milling, including improved accuracy, reduced costs, and accelerated design-to-production times, make it an ideal choice for marine projects. Ultimately, the success of these projects depends on the precision, reliability, and collaboration of all stakeholders involved. By prioritising these factors, manufacturers can ensure the delivery of high-quality, reliable components that meet the exacting demands of marine environments.