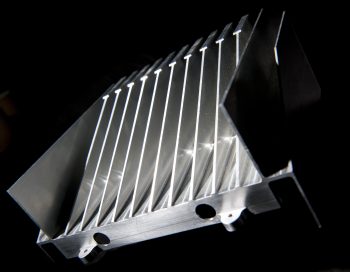
High-precision CNC machining is a computer numerical control (CNC) manufacturing process that uses computer-controlled machines to remove material layers from a workpiece, creating highly accurate and precise parts. In the electronics industry, high-precision CNC machining plays a vital role in producing custom components that meet strict industry standards. Precise components are essential in electronics as they ensure proper fit, form, and function, ultimately affecting the overall performance and reliability of electronic devices.
From smartphones to aircraft systems, high-precision CNC machining helps create intricate parts that enable these technologies to operate efficiently and effectively. With its ability to produce complex shapes and exact tolerances, high-precision CNC machining has become an indispensable tool for electronics manufacturers, allowing them to innovate and push the boundaries of technology.
The Role of High-Precision CNC Machining in Electronics Production
Bespoke enclosures machined from solid billets
In the electronics industry, customisation is key to creating unique and innovative products. High-precision CNC machining allows for the creation of bespoke enclosures machined from solid billets, providing unparalleled accuracy and precision. This process offers numerous advantages, such as improved durability, strength, and aesthetic appeal. The use of CNC machining for enclosure production is particularly beneficial in industries such as aerospace, defence, and medical devices, where high-quality and reliable components are paramount.
Prototype heatsinks
Heatsinks are a crucial component in electronic devices, serving to dissipate heat generated by electronic components and prevent overheating. Prototyping is an essential step in the development of new electronic products, and CNC machining enables rapid and accurate prototyping of heatsinks. This process allows engineers to test and refine their designs quickly and efficiently, ensuring that the final product meets all requirements and specifications.
Other intricate electronic components
In addition to enclosures and heatsinks, high-precision CNC machining can be used to produce a wide range of other intricate electronic components. These include PCBs (Printed Circuit Boards), connectors and switches, LED housings and optics, RF shielding components, and custom parts for specific industries such as automotive and telecom. The versatility of CNC machining makes it an ideal solution for producing complex parts with tight tolerances, surface finishes, and advanced materials.
Finishing Techniques Used in High-Precision CNC Machining
Precision masking
Precision masking refers to the process of applying a protective coating to specific areas of a part during the machining process. There are several types of masking techniques used in CNC machining, including tape, paint, and plasma etching. Precision masking is critical in applications where EMI shielding or visual appeal is important, such as in the aerospace and defence industries.
Conversion coatings
Conversion coatings are thin layers of material deposited onto a substrate through chemical reactions. They offer several benefits in electronics production, including corrosion resistance, wear resistance, and enhanced appearance. Common types of conversion coatings used in CNC machining include anodising and electroplating.
Hard and sulfuric anodising
Anodising is an electrochemical process that thickens and toughens the natural oxide layer on aluminium surfaces. Hard anodising creates a dense, abrasion-resistant coating, while sulfuric anodising produces a thicker, more porous coating. Both types have their own set of applications, but they share similarities in their excellent corrosion resistance and durability. Aerospace and medical device manufacturers often use anodising to enhance the performance and lifespan of their products.
Electroless nickel plating
Electroless nickel plating is a non-electrolytic process that deposits a uniform layer of nickel onto metal substrates. It offers several advantages, including excellent corrosion resistance, hardness, and lubricity. Electroless nickel plating is commonly used in the production of connectors, contacts, and other components that require high conductivity and low friction.
Gold plating
Gold plating involves the deposition of a thin layer of gold onto a metal substrate through electroplating. It provides excellent corrosion resistance, conductivity, and visual appeal, making it popular in the electronics industry. Gold plating is commonly used in connector and contact manufacturing, as well as in RF shielding applications where its high conductivity helps reduce interference.
Benefits of High Precision CNC Machining in the Electronics Industry
High precision CNC machining offers several benefits to the electronics industry, including improved product quality and reliability. By utilising computer numerical control (CNC) machines, manufacturers can produce components with extreme precision, resulting in higher quality products that are less prone to failure. This level of precision also allows for reduced production time and costs, as it eliminates the need for manual labour and minimises waste. Additionally, CNC machining increases efficiency and scalability, enabling manufacturers to produce large quantities of components quickly and accurately. Furthermore, the use of CNC machining allows for enhanced customisation and flexibility, enabling manufacturers to produce unique and complex components that meet specific customer requirements.
As the demand for cutting-edge electronic components continues to grow, the importance of CNC machining will only increase. At Thompson Precision, we pride ourselves on our commitment to delivering high-quality, precision-machined components that meet the evolving needs of the electronics industry. We invite you to explore our services and capabilities and consider us for your CNC machining needs.