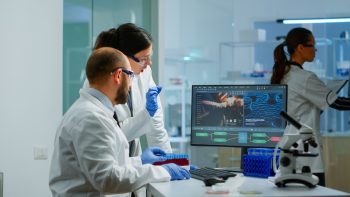
From minimally invasive surgical tools to the latest diagnostic scanners, modern healthcare depends on components that are machined to micron level tolerances. A single imperfection can compromise patient safety, disrupt regulatory approval, or delay time to market. That is why medical OEMs and life science researchers increasingly rely on precision engineering partners who combine advanced manufacturing technology with deep material and design expertise.
Thompson Precision – the sister company of JH May – has been at the forefront of high accuracy machining for decades, and today offers a fully integrated service for medical and pharmaceutical innovators.
Why Accuracy Matters in Healthcare
Medical devices are unique in that they must perform flawlessly inside or around the human body:
- Patient safety: Sharp edges, burrs or dimensional drift can damage tissue or lead to infection.
- Regulatory compliance: ISO 13485 and FDA guidelines require documented, repeatable processes.
- Performance & longevity: Orthopaedic implants, pump rotors and imaging gantries all demand tight tolerances to avoid premature wear and calibration drift.
Achieving this consistency at scale calls for advanced CNC strategies, real time inspection and a culture of continuous improvement – the hallmarks of precision engineering.
Thompson Precision’s Medical Engineering Toolkit
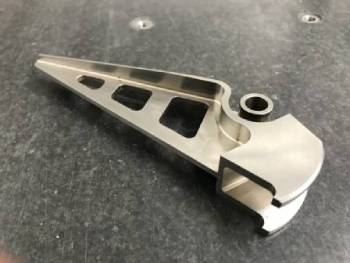
High Precision Component CNC Machined from Solid
Stainless 316
Specialist CNC Machining of Metals & Engineering Plastics
Thompson Precision keeps aluminium, stainless steel, titanium and other biocompatible alloys – plus high performance polymers such as PEEK and PSU – in stock, enabling same day programming and cutting for urgent prototyping runs.
5 Axis Capability for Complex, One Setup Parts
Five axis machines simultaneously move the cutting tool along three linear and two rotary axes, allowing surgeons’ instruments, implant geometries and diagnostic housings to be milled complete in a single clamping. The technology eliminates multiple setups, improves surface finish and removes cumulative error – critical when tolerances dip below 10 µm.
Low Volume Production & Rapid Prototyping
Because breakthrough medical products rarely launch at automotive volumes, Thompson Precision offers flexible batch sizes from one off research fixtures to a few hundred production parts. Low volume CNC milling bridges the gap between proof of concept and full automation while maintaining medical grade quality
Integrated Design & Engineering Support
In house mechanical design and engineering consultancy de risk projects early by:
- advising on material selection and surface finishes suitable for sterilisation;
- applying Design for Manufacture (DfM) to lower unit cost; and
- running finite element and tolerance analysis before a single chip is cut.
Speeding Up R&D Cycles
Time to clinic can be the difference between commercial success and a missed market window. With more than 70 years of consultancy experience – and the ability to ship time critical components in as little as 12 hours – Thompson Precision compresses development timelines without compromising accuracy.
Typical turnaround workflow:
- Concept review (Day 0): NDAs signed, datasets exchanged.
- CAM programming & proof simulation (Hours 0 6).
- Machining & in process inspection (Hours 6 20).
- CMM verification & surface finishing (Hours 20 30).
- Dispatch by dedicated courier (Hour 36).
Case Snapshot – Carbon Fibre Diagnostic Housing
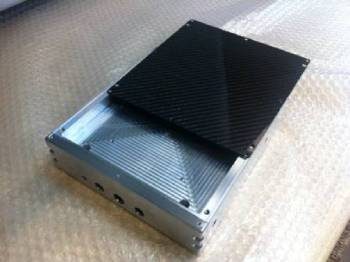
Medical Diagnostic Equipment Housing with Carbon
Fibre Lid
A leading imaging OEM approached Thompson Precision for a lightweight but rigid enclosure for a next generation MRI coil. The solution combined a carbon fibre lid with an aluminium base plate, CNC milled from solid billet to a ±0.02 mm flatness requirement. The hybrid assembly reduced overall scanner weight by 18 %, enabling faster patient positioning and lower energy consumption.
Quality Assurance & Compliance
Thompson Precision’s quality management system tracks every job from raw material certificate to final inspection report. Key controls include:
- Coordinate Measuring Machine (CMM) verification to < 5 µm
- ISO certified calibration of gauges and tooling
- Material traceability & full documentation pack for regulatory submissions
Future Directions in Medical Manufacturing
- Hybrid manufacturing: Combining CNC subtractive accuracy with additive freedom to build conformal cooling channels or patient specific implant lattices.
- Miniaturised robotics: The next wave of micro surgical tools will require even tighter positional accuracy, pushing tolerances into the sub micron domain.
- Digital twins & data driven QC: Inline sensors feeding process data into predictive models will cut scrap and accelerate validation.
Why Partner with Thompson Precision?
Advantage |
What it means for you |
70+ years of engineering heritage |
Lessons learned across aerospace, motorsport & scientific sectors applied to medical challenges. |
Dedicated medical & pharma cell |
Segregated tooling and inspection to safeguard biocompatibility. |
Fast CNC turnaround |
Stay ahead of clinical trial or investor milestones with parts in days, not weeks. |
End‑to‑end service |
From rapid prototypes to low‑volume production and ongoing optimisation. |
Precision engineering is no longer a supporting act in healthcare – it is the enabler that turns bold clinical concepts into life changing realities. Whether you are refining a drug delivery wearable, developing imaging hardware, or scaling an implant portfolio, Thompson Precision’s blend of advanced machining, rapid response and consultative expertise can help you deliver safer, smarter products – faster.
Ready to accelerate your medical innovation? Contact the Thompson Precision medical engineering team today on +44 (0)1277 365 500 or email [email protected].