The Solution
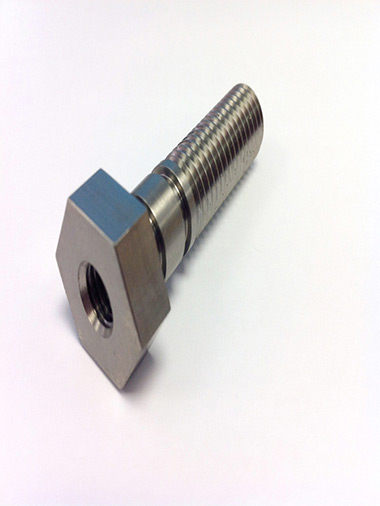
We were provided with both 3D data and manufacturing drawings for the component, which was then passed onto our purchasing department to order the material for the job. During this time one of our many CNC engineers could start work setting up the first turning operation. To manufacture the bolts, both CNC lathes and CNC milling machines would have to be used.
With the material delivered and the data imputed into the CNC lathe, the first bolt was machined; once this operation was complete, the bolt was passed to our inspection department. All the relevant dimensions were then checked against our client’s drawings to ensure the component’s accuracy. With the inspection department’s approval, the CNC turning operations were completed and inspected. As the order was for 300 to be manufactured, constant checks were performed during production to ensure the component stayed within the required tolerances and would meet our client’s high standards.
Time for the Milling to Begin
Once all the turning on the component was complete, the milling could begin. The 3D data was imported into our CAM software PowerMill, where the machining tool paths could be created, along with the required tools being entered into the programme. This allowed our engineer to run a simulation within PowerMill to visually see how the component will look once machined. The component was then manufactured on one of our CNC machining centres,with a final inspection done on the finished part. After manufacture and inspection, the bolts were bagged individually to stop the threads being damaged in transit, securely packaged and transported to the client.